It’s a fact about the oil and gas industry that if you order a 1-billion-dollar topside for an oil platform today, the following will most likely happen:
-
You will have it delivered to a quayside with a punch list and some unknown problems approximately 36 months from now
-
You will probably exceed your initial budget through incurred modifications and corrections by the time you are done inspecting the newly delivered asset
-
During the 36 months, anywhere between 100 to 3,500 people will be employed to design, procure equipment and materials, and construct the asset
-
Not all of those 3,500 people will have an up-to-date view of the current information, resulting in information logistics friction
-
You will use thousands of documents, emails, 3D models, phone calls, and meetings as the primary vehicles for carrying information about the asset you’re building
-
Not everyone will have access to the rapidly changing 3D CAD model that shows the asset geometry and layout. Not everyone will have access to SAP to look at procurement packages. And even if every user had access to to the relevant application, they wouldn’t have the time or the ability to go through every single application to understand what’s going on.
These are some examples of inconsistent information flow that lowers productivity for the oil and gas industry. People make decisions based on missing and unreliable information - some of which may be up to date, some two days old, and some maybe even a week old. The result? Different perceptions among the involved parties regarding the current state of the project, significant effort expended to agree on what the actual state is, and management risking their operations based on a time-delayed picture of the situation.
Sharing and collaborating in one place
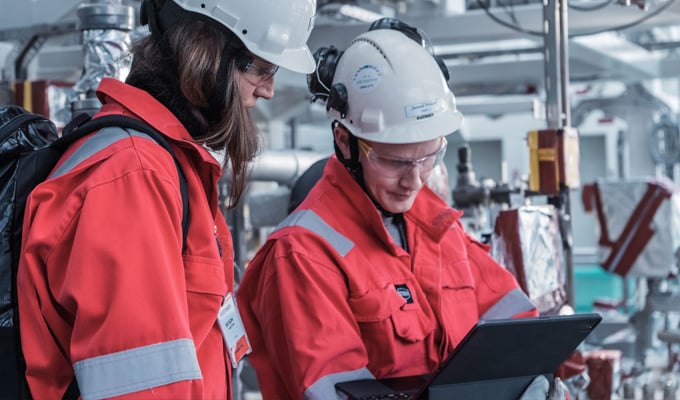
To get a real-time picture, you can collaborate in Aize. Aize collects and aggregates the relevant information, lets you navigate the relationships between the pieces of information and creates a model representing your asset. Everyone with access can then view the model together in real time, search it, navigate it and comment on it to gain a collective understanding of the actual state of the asset.
How does it work in practice? Once you find an issue that needs to be solved, instead of leaving Aize to send emails, find documents, and get the engineers to provide screenshots from the 3D model, you start working the problem right there. You add comments, share an easy-to-understand view of the problem, let people look at it on their laptop or tablet, start a discussion, and agree on the most effective solution, storing the debate for later reference.
For instance, if you are responsible for constructability checking, and you find a problem, Aize helps you avoid the following:
-
You don’t need to send emails with attached snippets of the 3D model
-
You don’t need to call for a meeting between engineering and construction
-
You don’t need to spend hours arguing and comparing different printouts and design specs side by side before finally agreeing on what to do
With Aize, engineers and construction workers can look at, discuss, understand and often solve the problem in near-real-time and add to the discussion as the problem-solving moves forward. It’s using technology that you’re accustomed to in your everyday life as a private citizen, brought to the world of asset design and construction.
Being developed for and deployed to the largest project on the Norwegian Continental Shelf
We are currently deploying Aize in the NOA project, a development of the southern part of the North of Alvheim Krafla-Askja area. It’s one of the largest remaining oil and gas fields offshore Norway. It’s also the largest and most complex project on the Norwegian Continental Shelf. Therefore, Aker BP, its primary operator, needs to collaborate better and make accurate decisions faster to succeed. Our Senior Customer Success Director, Rósa Stensen, will be working closely with Aker BP in the upcoming years to embed and foster collaboration throughout the entire project. Here is her impression so far:
“Given how digitised our day-to-day lives have become, I think people would be surprised if they knew how far behind we are in the way we work with EPC projects. One example of this is documents. We produce a massive number of documents. And when collaborating with vendors across the value chain, documents are sent back and forth for review. When you’re dealing with a major project where the value chain is composed of hundreds of suppliers, there is significant potential for savings by moving away from documents to structured data and taking advantage of the available digital technology.”
Do you have any questions?
We would love to hear from you. Feel free to reach out to us at any time.
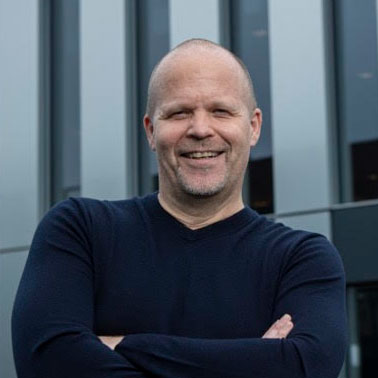
Post written by Frode Strand
Working as the CTO at Aize, Frode brings decades of experience from software development for multiple industries, through IT strategy work for international companies, to IT management experience for EPC companies, to the world of trying to make technology count. Always interested in understanding the structure of any given problem, and thinking the elements that might constitute a solution, Frode is known for engaging with gusto and energy, turning inquiry into ideas, and working to articulate the essence of the task at hand. Curious well beyond his capabilities, Frode is also an avid consumer of literature on physics, math and computer science. Frode holds a degree in Computer Science from NTNU.
Stay in the loop
I’d like to sign up to Aize newsletter